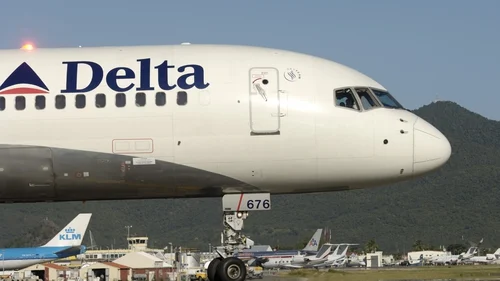
Rosemary and Larry Brester have been operating Hobart Machined Products since 1978, using metal milling and grinding techniques to produce aircraft components. Hobart is one of many suppliers located around Puget Sound in Washington state that serve Boeing, and the Bresters had intended to double their four-person workforce to meet Boeing’s demand for increased production of its best-selling 737 jets. Hobart supplies parts to larger companies that sell directly to Boeing.
However, these plans are now uncertain due to U.S. regulators reducing Boeing’s production rate following a mid-air panel blowout. The incident has caused further mistrust and financial pressure on Boeing’s most vulnerable suppliers, some of whom may close if the company’s problems persist. Rosemary Brester expressed concern, noting that they purchased new equipment to facilitate growth and delivery schedules, and other companies in the region and around the world likely did the same.
Boeing’s recent crisis began with the panel blowout on an Alaska Airlines flight on January 5th. Federal investigators are still determining the cause of the incident, which led the U.S. Federal Aviation Administration to limit Boeing’s production rates. Many suppliers have been struggling due to a pandemic-induced slump in demand, along with a previous 20-month grounding of Boeing’s 8 that temporarily halted production. For some, the January 5th incident also reduces optimism for payback sparked by the recent travel boom that revived aircraft orders.
Aircraft parts must be ordered up to a year in advance. Many suppliers added employees and materials or have been running at faster production rates, expecting to be paid later in the year. Now, they face an inventory build-up that will eat up cash. The FAA’s order allows Boeing to continue producing MAX jets but not increase its current monthly rate until the agency is satisfied that quality-control issues uncovered during the probe are resolved. The FAA did not specify the number of planes Boeing can produce each month, and Boeing has declined to confirm its current monthly rate, creating confusion over the cap.
Boeing had previously stated that 737 production would reach 38 per month by the end of 2023. In a January 22nd email seen by Reuters, it told suppliers to adhere to the master schedule that calls for an increase to 42 a month in February. One Boeing supplier stated that if the production cap is for a limited period, it could catch up on work on other aircraft programs. However, other suppliers would likely view the cap as a “pretty big problem.”
The uncertainty is particularly harmful for smaller suppliers, who invest in working capital for announced production increases that do not happen. Glenn McDonald, a supply chain specialist at AeroDynamic Advisory, explained that “many suppliers were counting on rate increases in 2024, 2025. Over the last three or four years, even the trust of the supply base in Boeing’s rate announcements has been eroded.”
Spirit AeroSystems already faces financial pressure and relies heavily on the MAX program. Total 2023 aerostructure revenue from an index of suppliers like Spirit, GNK, and others is around 80% of 2018 levels, according to AeroDynamic. Spirit stated that it would continue to cooperate with the FAA and coordinate with Boeing.
TNT Aerospace, a family-run business in Sumas, Washington, considered joining the 737 program, but Boeing’s struggles have President Aaron Theisen thinking twice. “We need to make sure we have a strong foundation underneath the business to grow,” he said.
I don’t think the title of your article matches the content lol. Just kidding, mainly because I had some doubts after reading the article.